High quality custom guitars that are durable, stable, and comfortable.
My T92 model draws from tradition and is built one at a time, with exacting precision for a lifetime of enjoyment.
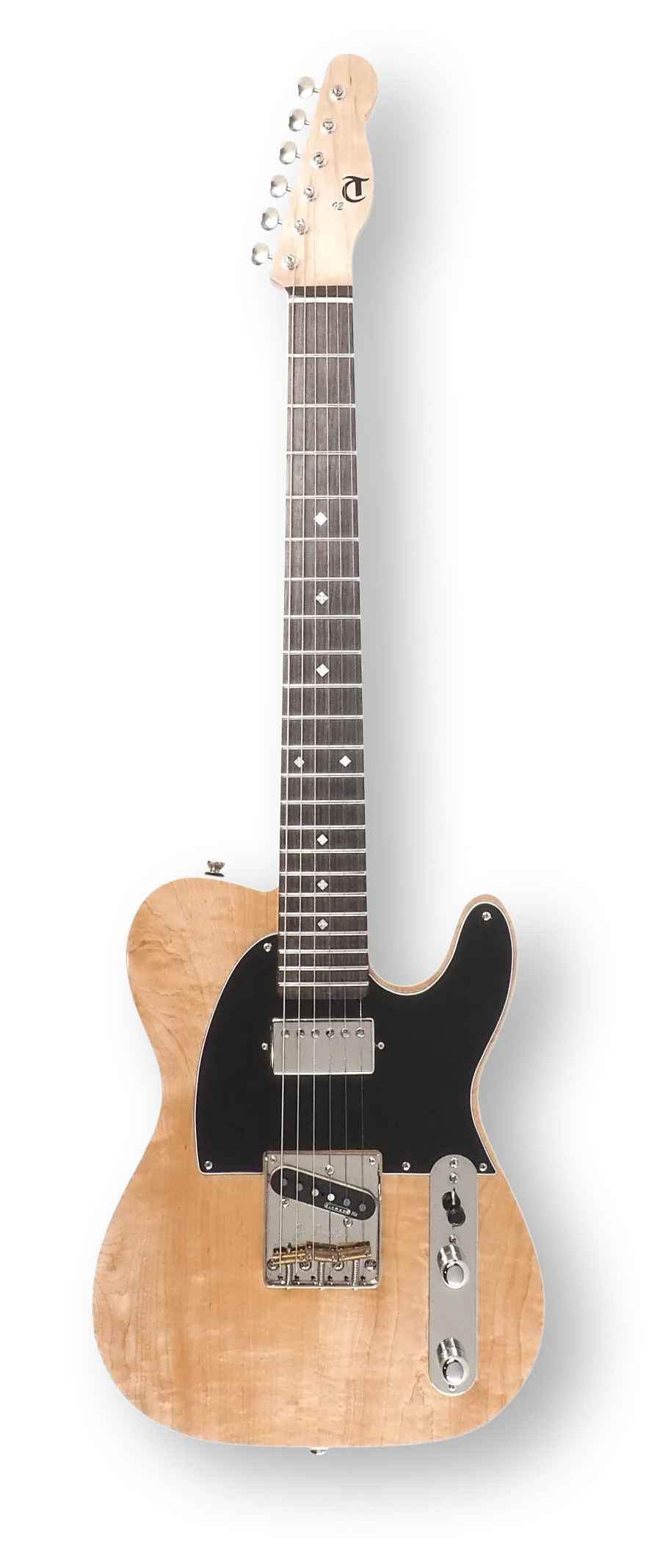
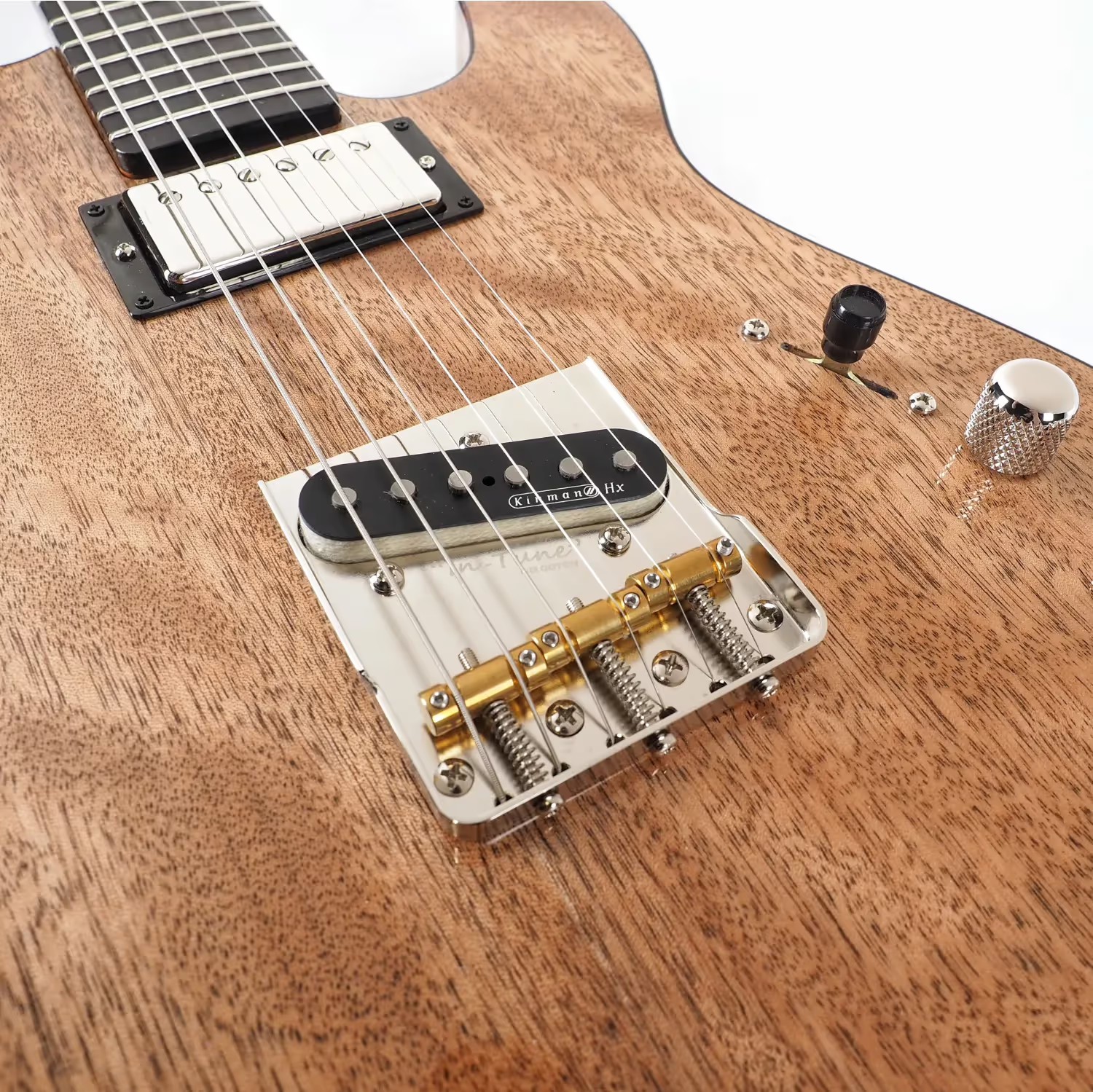
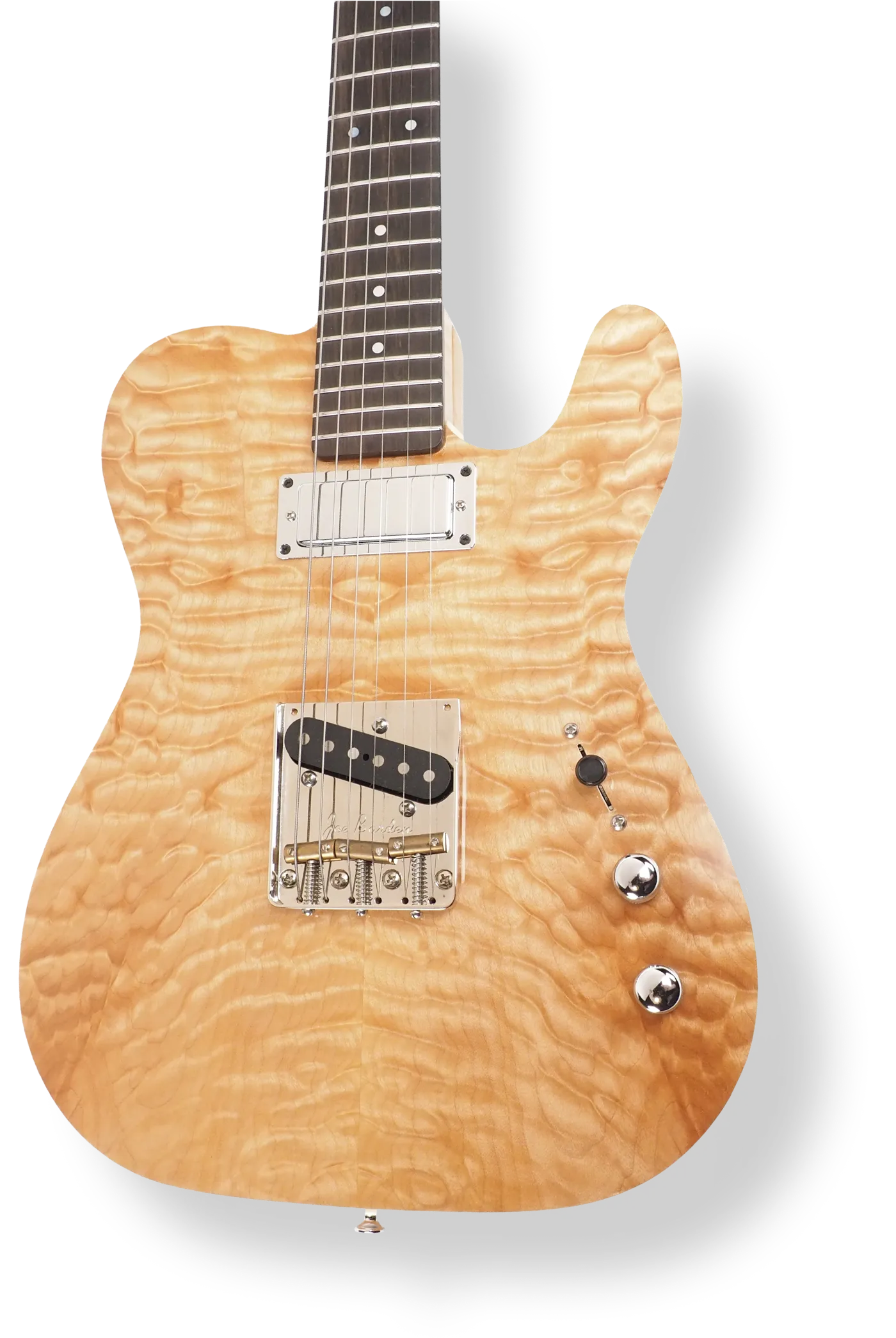
I have been building, performing, repairing, modifying, and restoring guitars for over 40 years.
I believe what is important to a performer is:
These are the tools to give the artist the ability to experiment and express their thoughts and emotions unhindered by one's instrument.
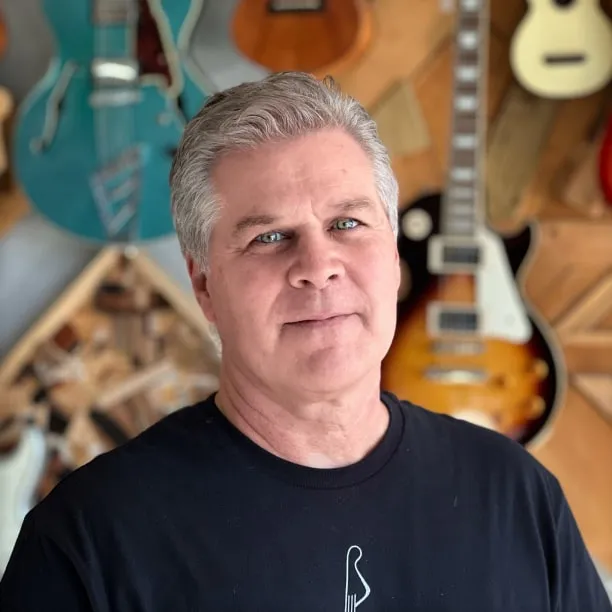
Ron Tracy T92
An overview of the T92, my signature custom model
The T92 specs
Guitar Body: Semi hollow chambered to reduce weight and emphasize a more acoustic tone, or solid body with comfort contours. Shapes and materials are optimized for comfort, playability and aesthetics.
Woods: Alder, cedar, ebony, mahogany, maple, rosewood, & walnut are my go-to choices.
Neck: 24.75" scale length, stainless steel frets. Hand shaped with a bone nut, 1.687" width for increased room for enhanced playability. Double action truss rods for precise neck adjustments.
Hardware/Electronics: All of the hardware I use and recommend is based on years of practical experience from building and playing guitars. I know what works, feels good, and stands the test of time.
Custom Options: I am open to custom options for any part of the build within reason, and will help you optimize every component based on my own experience and your needs.
Base Price: $3,000
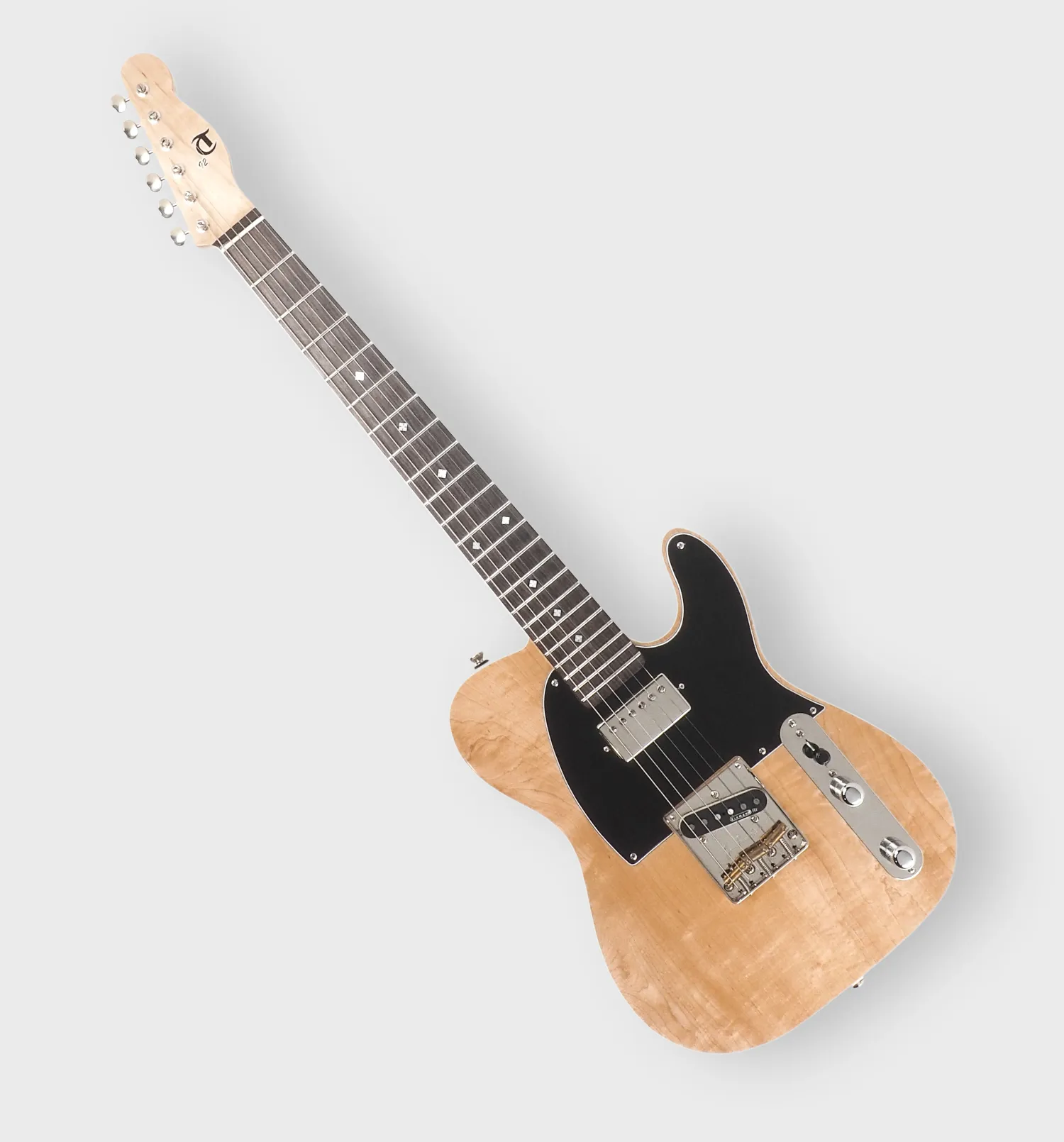
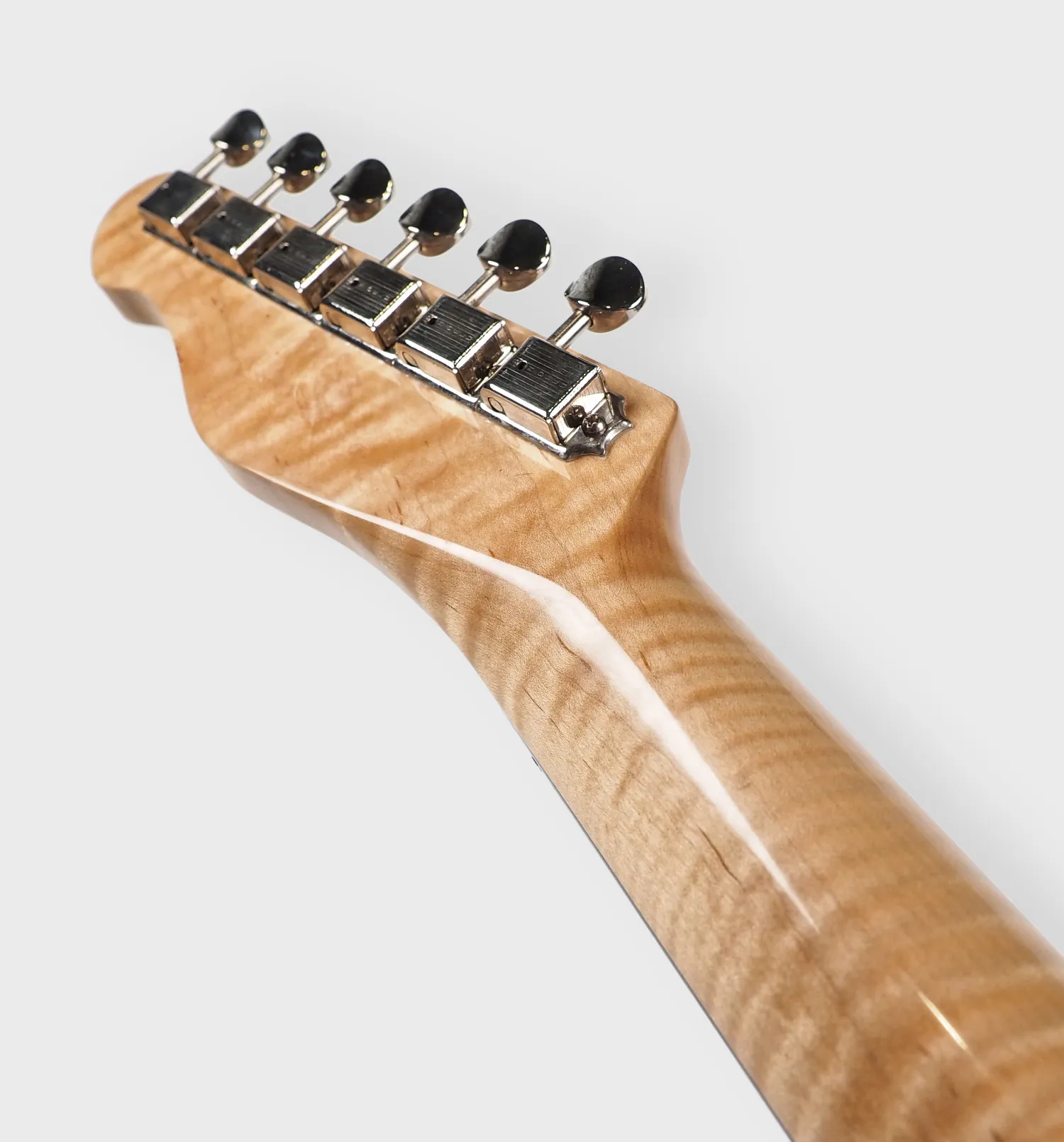
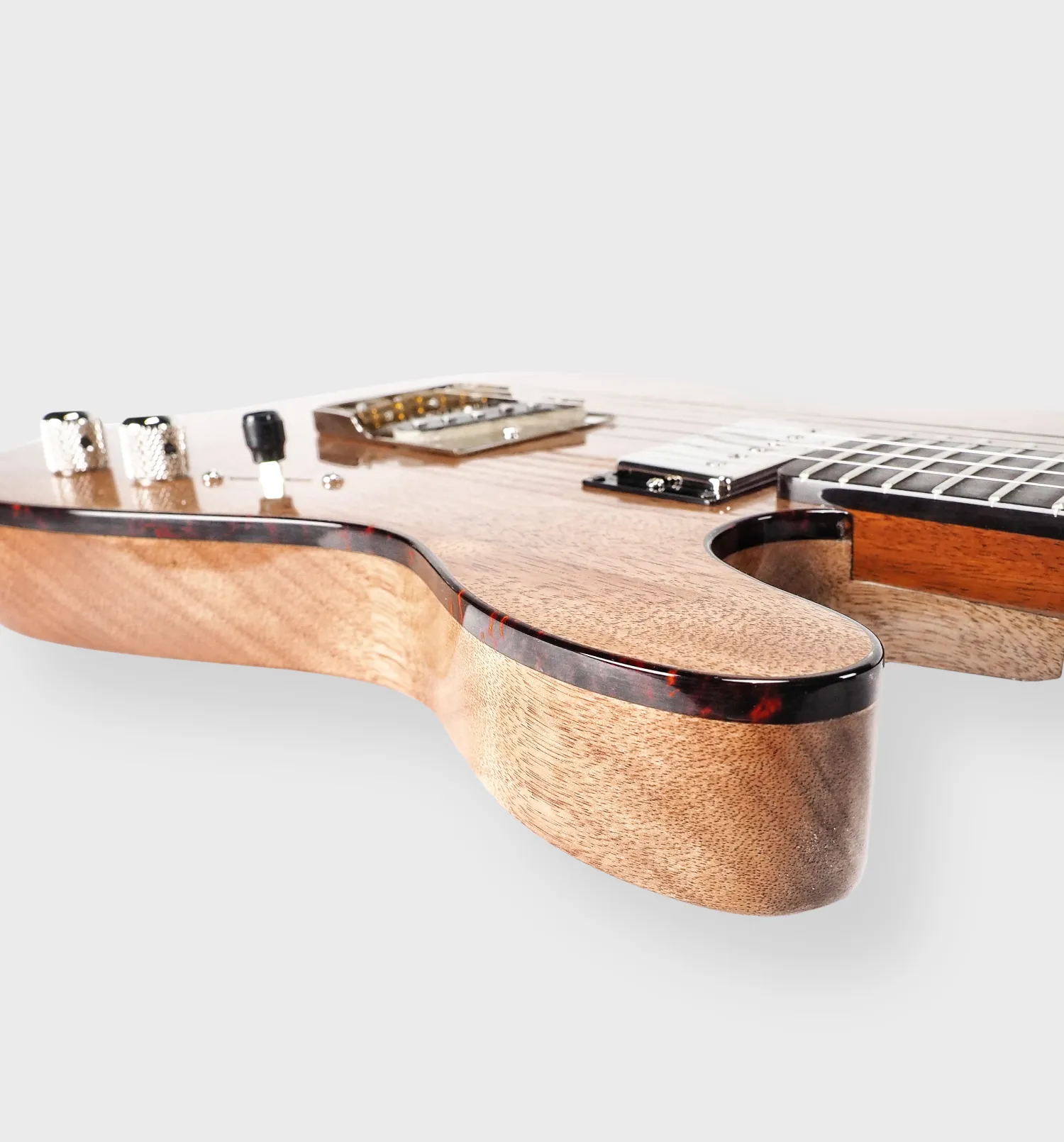
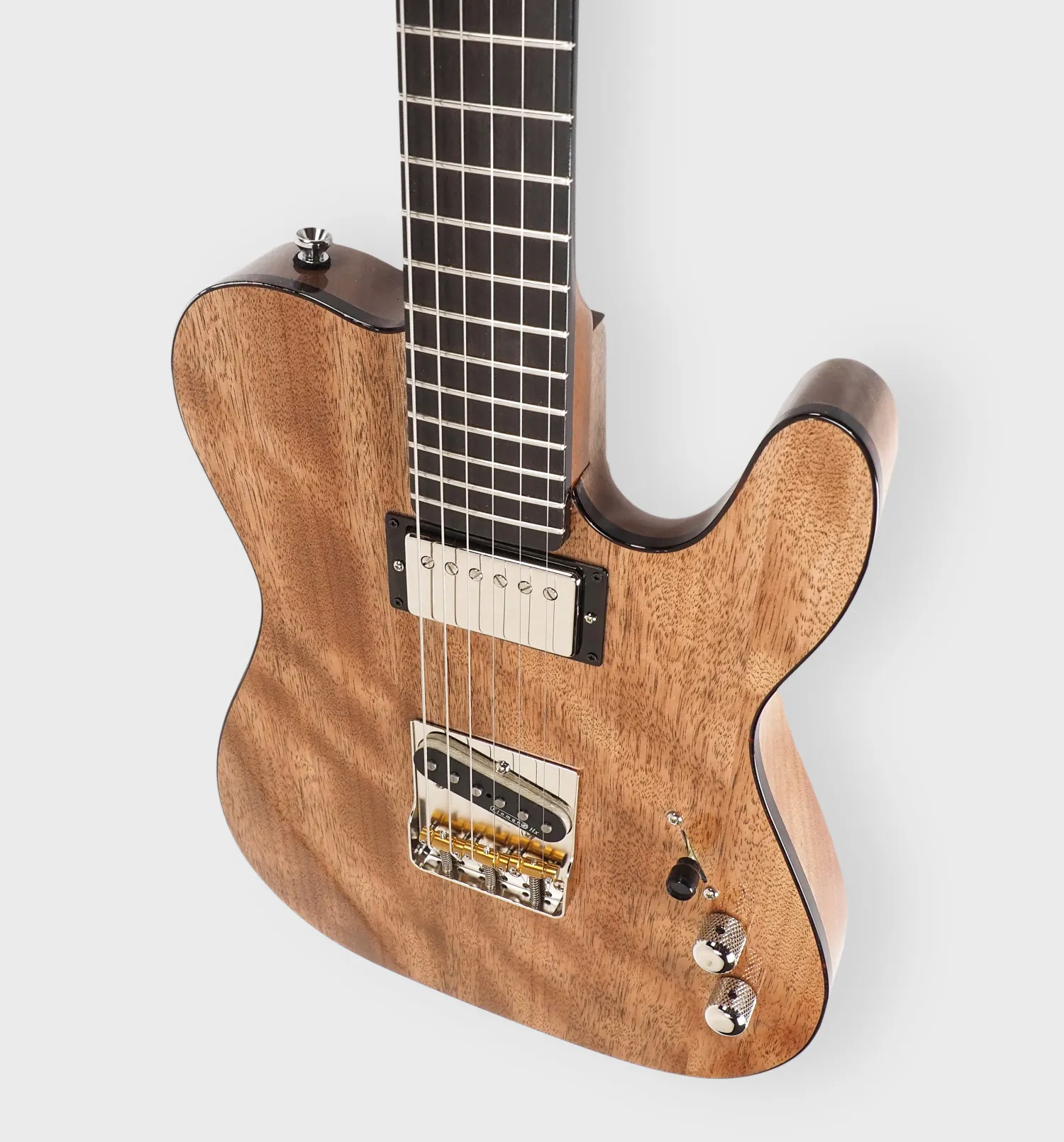
Solid Vs. Semi Hollow Bodies
Key differences that help you decide which is right for you
A solid piece of wood, dense & sustaining
Standard of the industry, slightly heavier with strong fundamental notes.
Traditionally a block with slightly rounded edges. Edges can be more rolled, with belly contours added, and a cutaway heel pocket contoured. All to add comfort against your body and ease of reaching the highest pitched notes.
The grain of the wood shows throughout the whole body.
Can be laid out traditionally with a control plate & pick guard or not, or rear routed to reduce the overall weight.
Recommended for use with single coil pickups. It includes shielding to help reduce noise and 60 cycle hum.

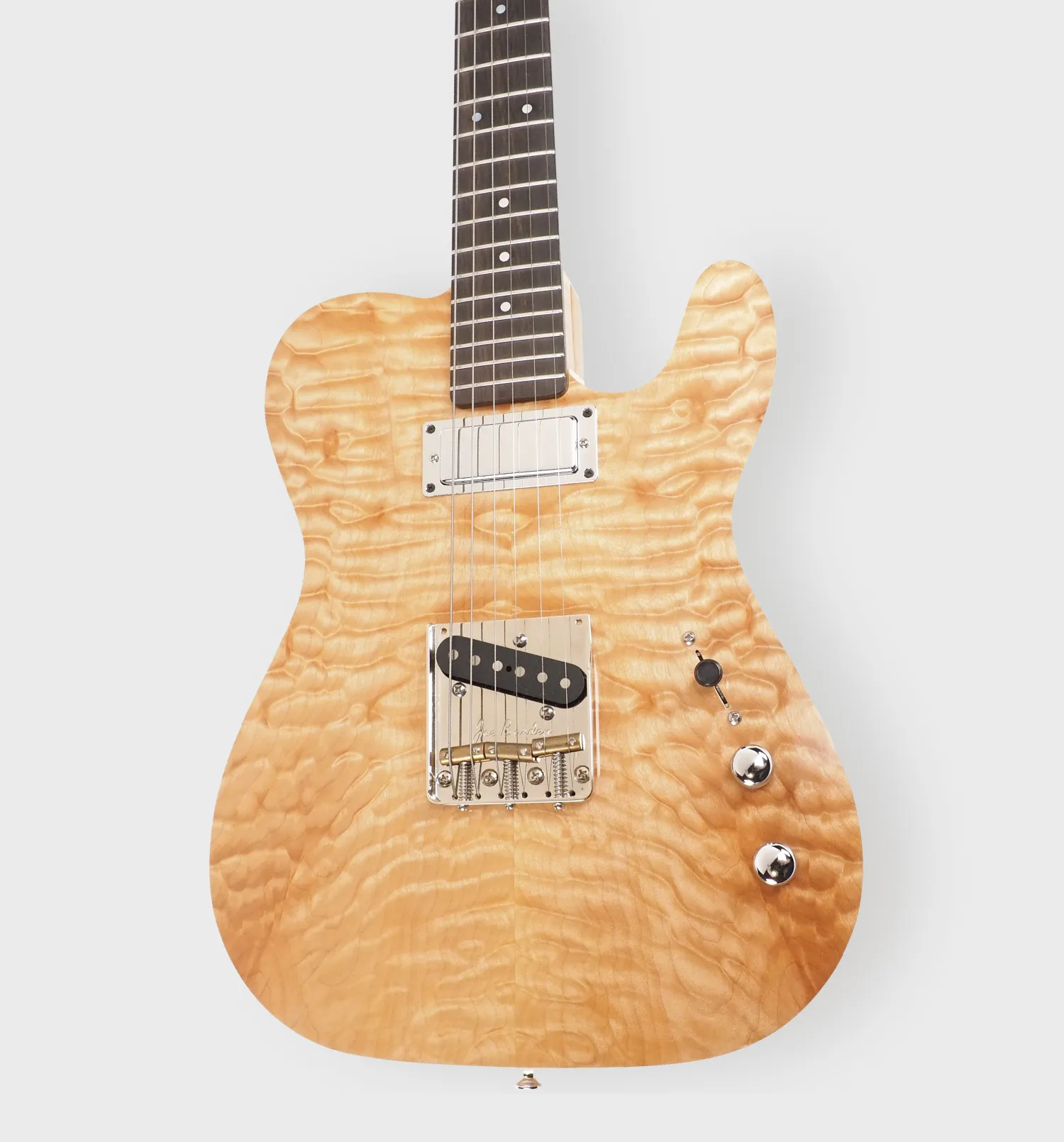
Routed Chambers in solid wood, and a cap wood
Lighter and resonant. The original body style I designed and have used for most of my builds.
A solid piece of wood with routed chambers and a cap wood—usually an alder core and contrasting top wood is used for a more stunning visual effect.
The chambers create a more acoustic overtone structure. No F hole—same theory as a BB King Lucille Model, to control feedback issues.
A cutaway heel contour is available. No belly contour on this one.
Typically a bound top to hide the glue joint for clean aesthetics
Can be laid out traditionally with a control plate & pickguard, or rear routed.
Recommended for anyone concerned with the over all weight of the guitar. Best with hum canceling pickups.
A look at my latest T92 build
A detailed look at the latest custom T92 build I've completed:
Click to enlarge
Why choose custom?
Truly handmade from design to completion. Attention to detail from start to finish by one individual. Total quality control.
No computer cut parts, no assembly line, no order department, no sales department, zero miscommunication.
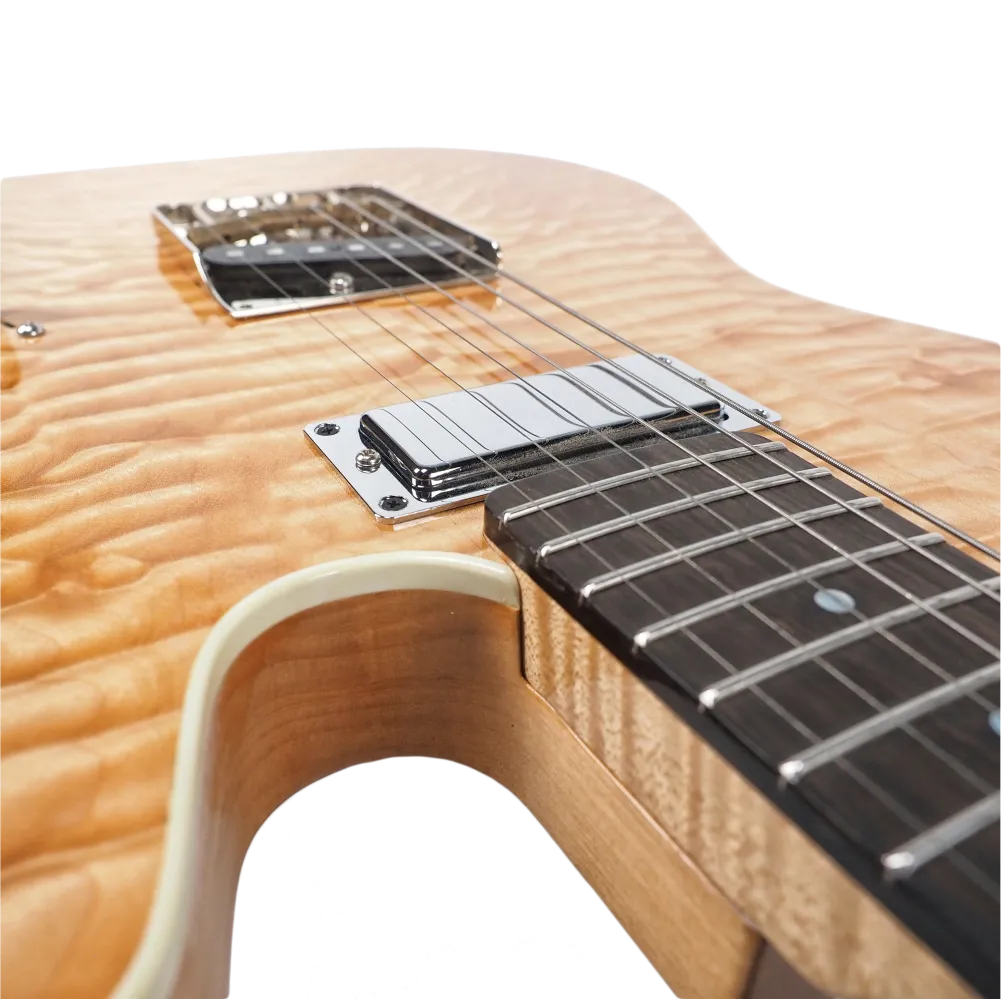
Comfortable Guitar Bodies
Comfort contours on solid bodies, or chambered bodies to reduce weight and give a more acoustic tone. Smaller size than traditional instruments by 8-10 percent. This adds to the comfort and aesthetic of the overall instrument.
The whole build from start to finish keeps comfort, tone, and playability front and center.
Precise & Playable Necks
Necks built with a 24.75” scale length with stainless steel frets. Hand shaped with a bone nut, 1.687 width for more room between the strings and less likely to slip off the sides of the neck during vigorous play. The truss rod is double action for precise neck adjustment.
The neck is crucial to the sound and playability, and I pay special attention to how it fits and interacts with the body.
Traditional & Exotic Sustainable Woods
The woods have been sourced and stashed over many years for these one of a kind projects. Along with new finds, only top quality woods are used in these instruments. Decades of experience go in to recommending materials for sound and aesthetic quality.
Some options include alder, cedar, ebony, mahogany, maple, rosewood and walnut.
Superior Electronics
Only the highest quality electronics are used including pickups by Lollar, Revel Custom, Kinman, Duncan, and DiMarzio.
Nitrocellulose Lacquer and Oil & Wax Finishes
Most of these builds have nitrocellulose lacquer, a very traditional finish. Oil and wax finish is used for a more natural feel. Both bring out the natural qualities in the woods I use.
Fine-Tuned Setup
After the build is complete, a professional set up is included. This is a completely bespoke service, and every detail matters to me.
Custom Options
Just about every component is customizable, from fingerboards, inlays, hardware, and more—decades of experience help guide the process and get your guitar looking and playing exactly how you want.
Everything is made from scratch (except hardware and electronics), and finishing work is done in-house.
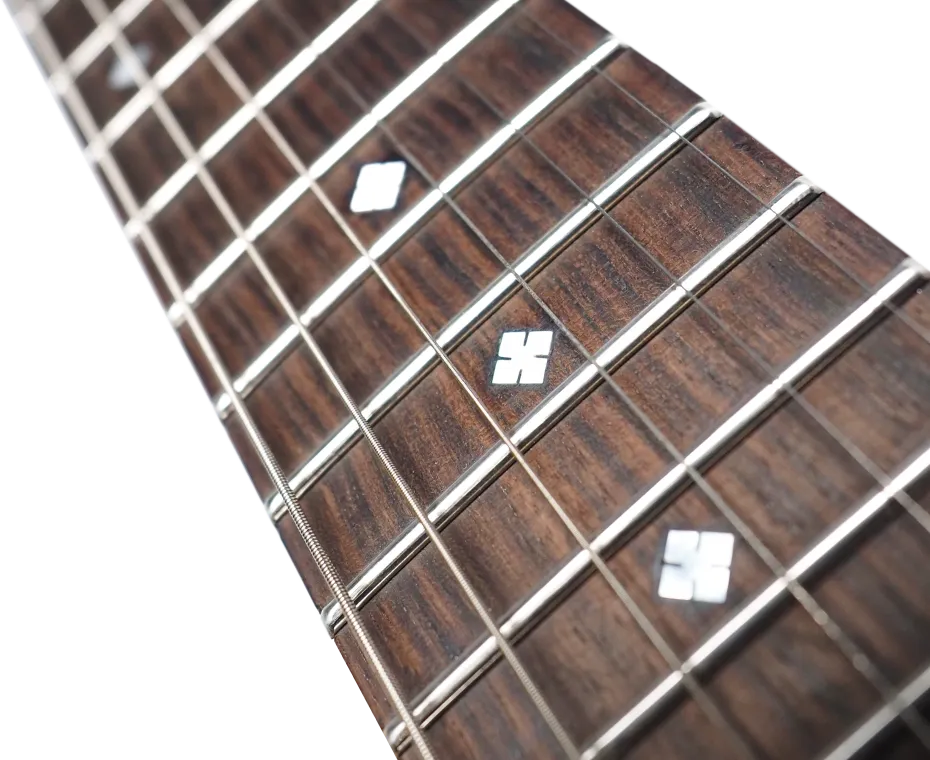
How to Start a Custom Guitar Project
What to expect, timelines, and an overview of the process from initial ideas to finished product
Reach out
Contact me! Email, call, or stop by the shop and let me know you're interested and we'll go from there.
Discovery
We'll talk about what you are looking for. I encourage you to share your ideas and ask any and all questions you may have about the process.
The Details
We'll go over what kind of woods, pickups/electronics and all the fun details that set a custom build apart.
Build it
After an agreed upon scope, I will start the build. 25% down payment is required, and I communicate with you throughout the process.
Complete it
A custom creation takes roughly 1 year to complete. I give you a rundown on proper maintenance & care and stand by my work.
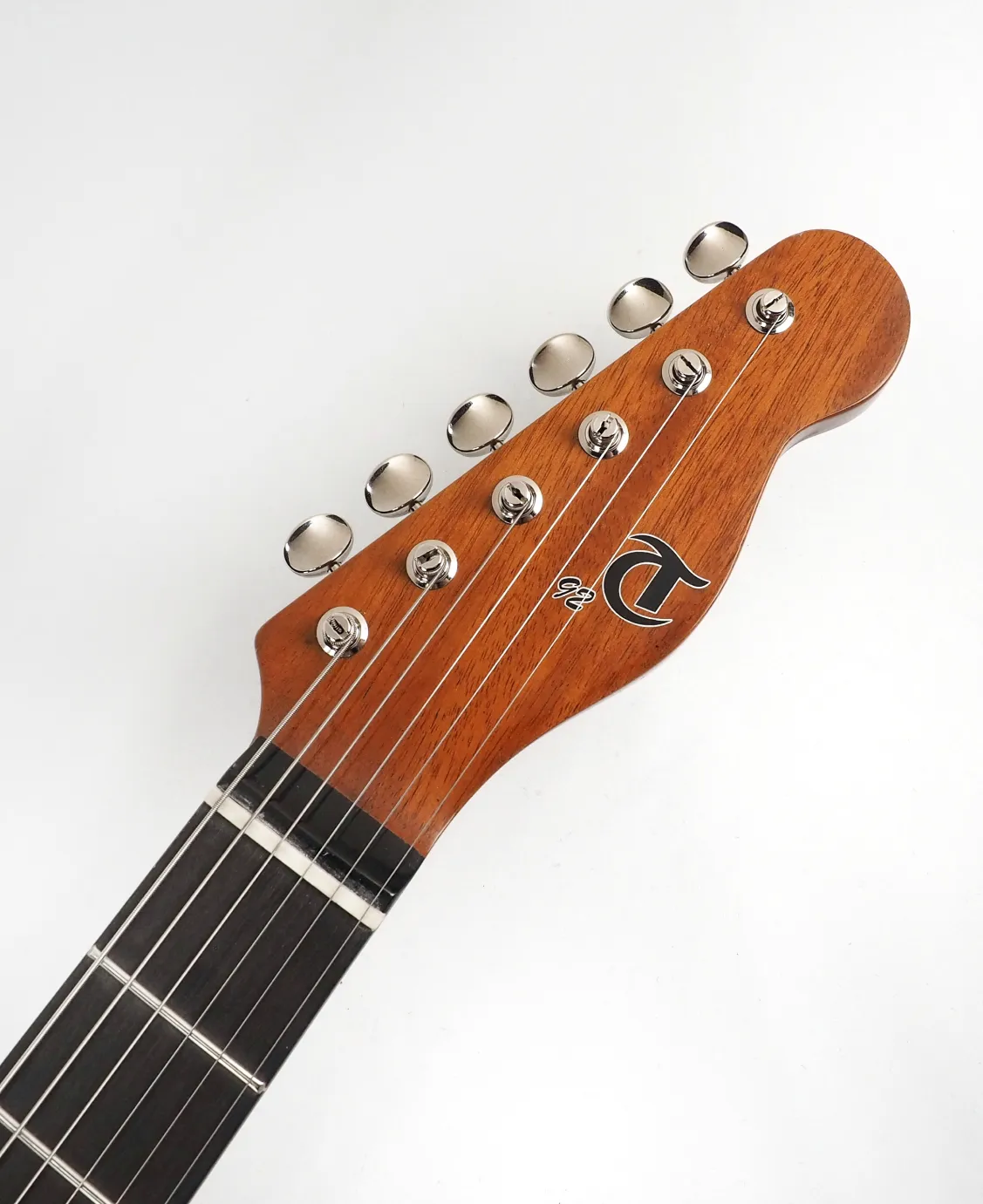
The Ron Tracy Process & Philosophy
I build the qualities into the guitar I would want to play. I build each guitar as if it was for myself.
The first prototype was made in 1992. I created a reduced size Fender body with a Gibson scale length neck, resulting in a guitar with exceptional tone and playability. I personally played this instrument for several years, on many gigs and experiments in recording. By modifying and tweaking it to achieve the perfect combination of all the components, I believe I have created an incredible instrument that would make any artist ecstatic. Each guitar is carefully planned out before starting, and constructed with exceptional care using all of my experience and knowledge. I attempt to make each guitar better than the last.
The wood choice and layout of the body design are the beginning; this is the resonating factor of the guitar. Then, the neck and fingerboard wood are selected to compliment the body wood. The neck work begins by slotting the fingerboard, rough tapering, and radiusing. It is laid out onto the neck wood blank. The truss rod slot is routed, and the two way truss rod is installed. I glue on the fingerboard and true the surface for the best possible playability and comfort, layout and shape the peghead, and shape the neck and fret—all by hand. No CNC machining here.
Next is the body thicknessing and layout. I fit the neck before anything else, as I believe the neck to body joint is crucial to overall sustain and tone of the guitar. They have to work together for optimum performance.
Next is routing out the chambers and gluing the top cap on before shaping the body. Once the neck has been fitted I route the pickup and control cavities, prepare and bind, or round over the edges and contour. Then sand, sand, sand to remove any scratches and prepare for finishing. Again, no robots or computers—just my hands and skills. I use nitrocellulose lacquer for most projects, as well as oil and wax finishes. Both bring out the natural quality of the woods. Assembly, adjustments, installation of all the parts and wiring all by my hands.
Lastly, is the setup and fine tuning. With over 40 years of expertise in making each guitar sing and come alive, this is the apex of the experience. All of this takes time, an exacting eye, skilled hands, and patience. One of the enduring factors of these guitars is that no two are exactly alike. Each one has its own voice and individual beauty.
Custom Guitar Gallery
A look at some custom T92 guitars I've built over the years
Click to enlarge
FAQs
Some common questions about starting a custom build
I have completed 52 guitars total. 30 are T92's.
About a year. This is a handmade instrument. Literally starting with blocks of wood, so it takes time.
I built my first guitar in 1979. The first T92 was made in 1992.
Starting price is $3,000. Depending on materials and design, prices vary.
A case is not included with the price, but I offer a Reunion Blues Gig Bag for $200